Integration (Week) Experiment Acceptance Process Review
Hello people,
Siiri (Electrical), Nik (Software), Jaka (Mechanics) and Fabian (Mechanics) are here. From the 9th to the 14th of December 2019, we went to the Integration Week in Bremen at ZARM (Zentrum für angewandte Raumfahrttechnik und Mikrogravitationsexperimente = Center for applied spacecraft technology and microgravity experiments) where we tried to integrate our experiment with the other ones into the REXUS rocket - not the actual rocket though but rather the infrastructure.

(Ofc we had to check out the Christmas market in Bremen in the evening and get some nice Glühwein to relax a little.)
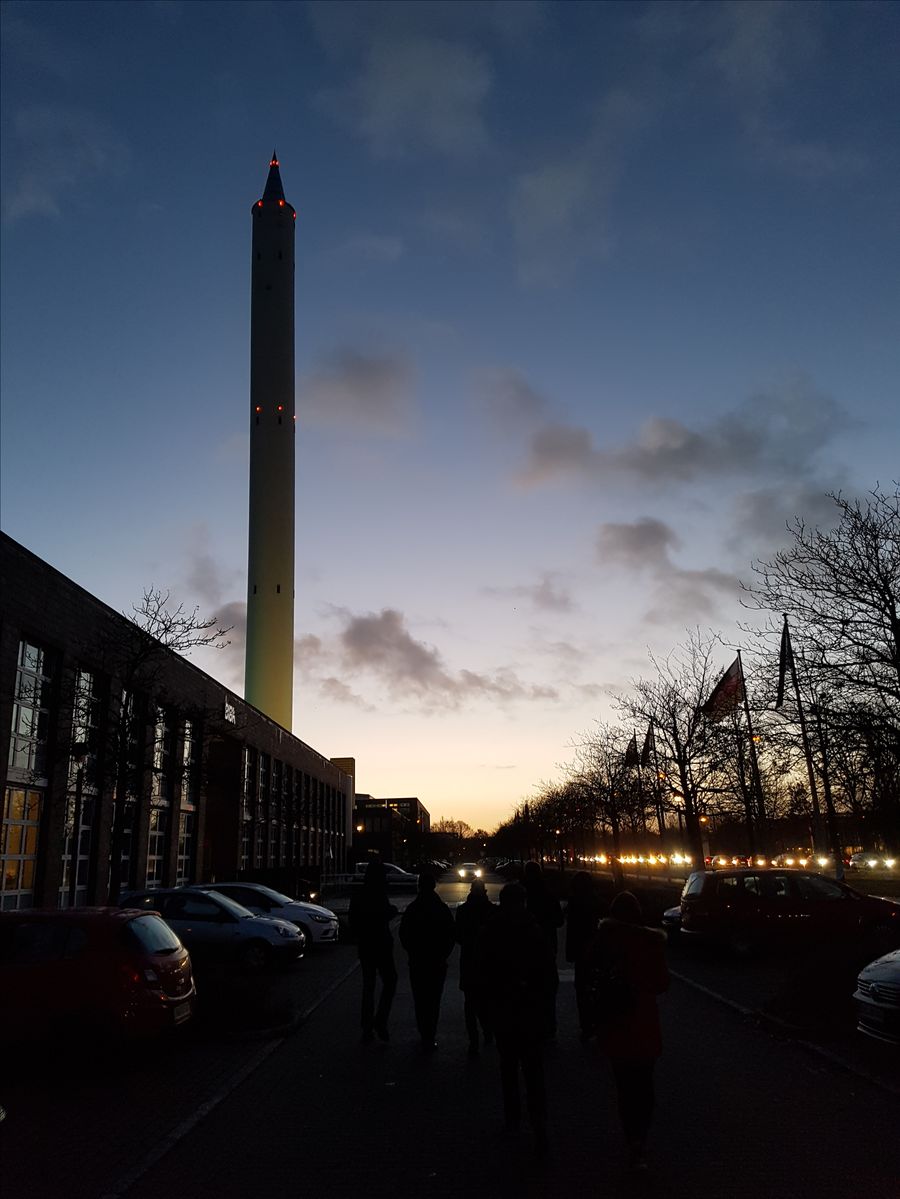
(The drop tower of ZARM where microgravity experiments are conducted. It's 150m tall.)
Tried? Yes, because from the beginning, like almost every team, we ran into some problems.

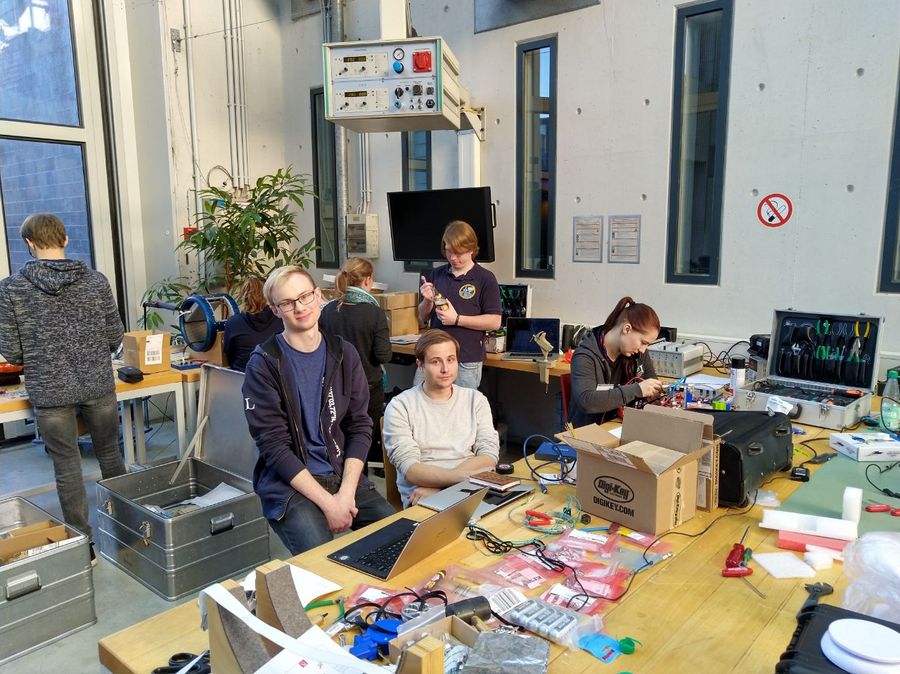
Our experiment has been shipped in time, supposedly, and should have arrived the week before on Friday, but as we arrived on Monday at ZARM, Dieter told us that our experiment hasn't arrived yet. Great. So we spend the first two days by calling DHL and postnord in Sweden, Germany and Denmark and we found out that the experiment got delivered to the wrong address in Denmark for some reason. You can see on Fabian's and Nik's faces that we were kinda bored and a little stressed because we wasted precious time doing not really anything - at least from the mechanical point of view. Nik and Siiri spend a decent amount of time on preparing the electronics (resoldering of cables etc.) and tweaking the software.

On Wednesday, the package with our experiment finally arrived, and it felt like assembling an IKEA cupboard or sth. (Ha haha because we are a Swedish experiment *ba dum tss*)
(face of the mechanicals)
Anyhow, we could finally start working for real and after a lot of small fixes to the outer structure (drilling new holes, widen holes and manufacture some extra parts for the ejection mechanism) we were ready to integrate our internal structure to the external one. To be precise, we were ready, Stefan wasn't because we had to do a full system test first, which means going through the full pre-launch and launch/flight time line and triggering all the necessary signals in all the experiments to identify errors in the system because until now, no team was able to test if their experiment would work with the other experiments in combination on the rocket, receiving and sending signals.
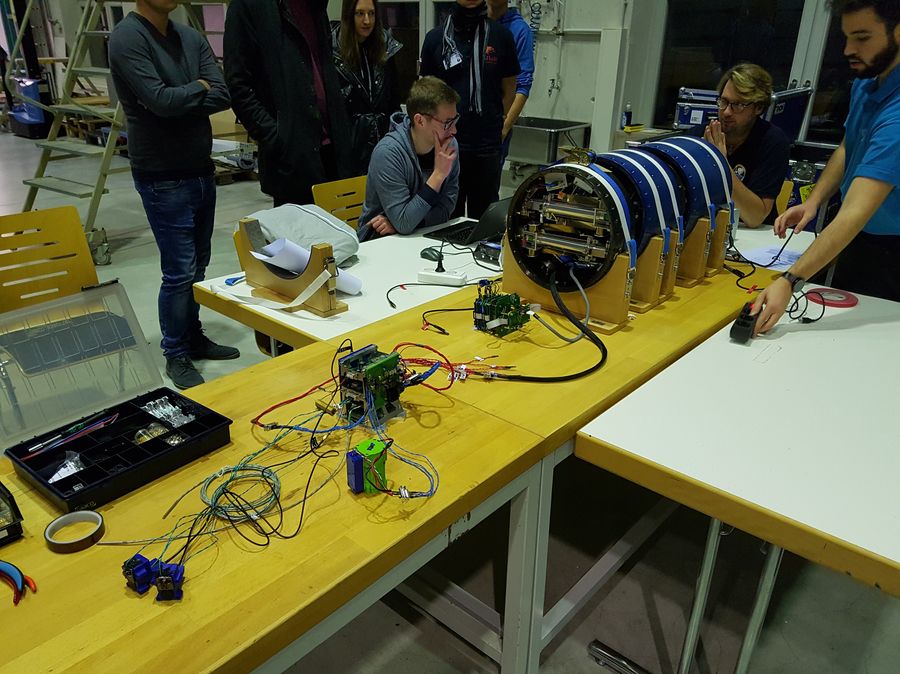
Even Stefan is praying that the test succeeds. Didn't help. Our PCB structure can be seen on the very left, above the green small box (batteries).
Good that we did that test, because we noticed that once we are unplugged from the REXUS power line and switch to our internal batteries, we give a lift-off signal to all the other experiments on the rocket. Which is bad. Really bad. After some confusion and more tests we weren't really able to identify the source of the problem and also the experts did not know where the error might stem from. So this is what we will spend time on in January.
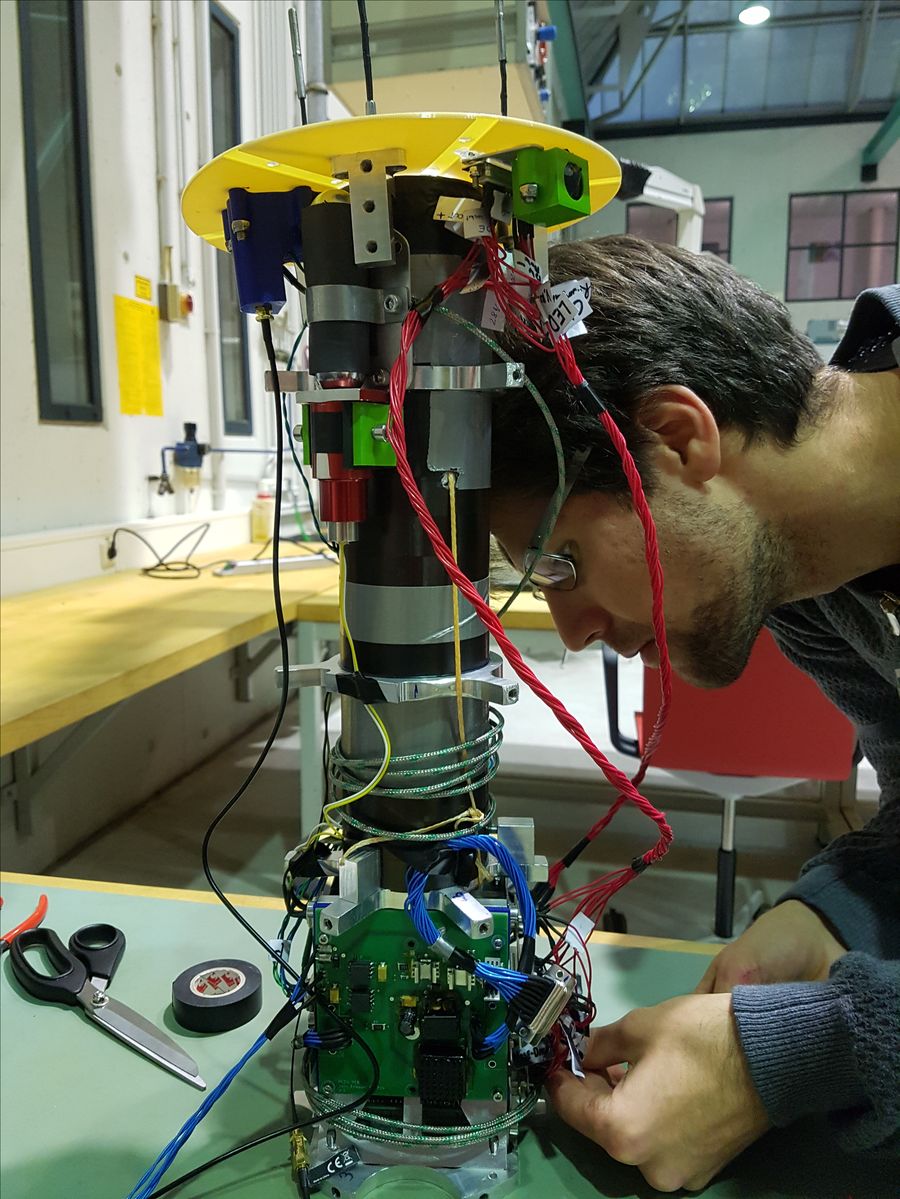
Here you can see the internal structure before it got inserted into the external carbon fiber cylinder. On the bottom there is the PCB structure which is attached to the internal cylinder, containing the main and drouge parachute. The orange string (Dyneema) holds back the spacer which separates the drouge from the main chute. The drouge chute is deployed by means of a CO2 system (middle upper left, red/green) which is triggered by gunpower. The gunpowder explodes and pokes a hole into the CO2 cylinder (covered by black rubber in the upper left, next to the blue camera housing), the CO2 gets directed into the internal cylinder and blows out the drouge through a piece of aluminum foil. The main chute is then deployed by cutting the Dyneema 10s later, by means of a pyro cutter. The rest of the picture are mostly cables...
The integration hasn't been always easy...
The integration hasn't been always easy...
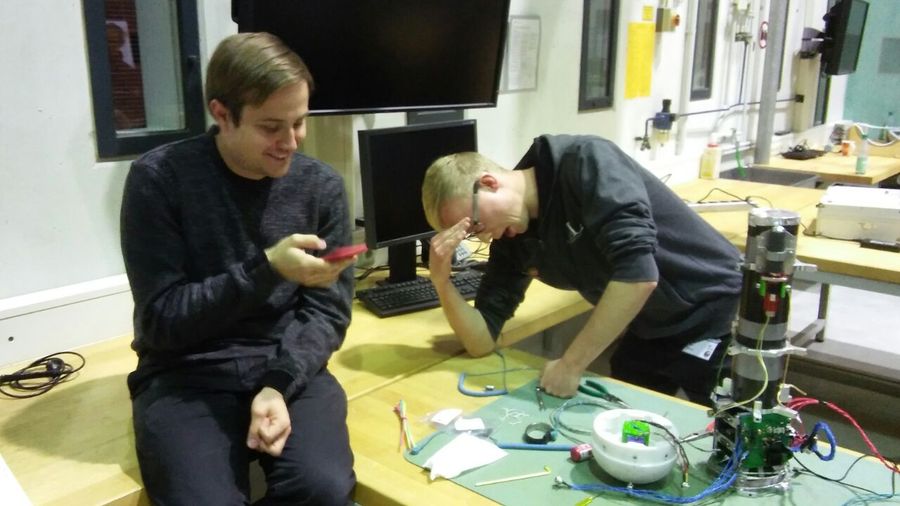
Once assembled (at like 1am in the morning), we left the experiment for the last stress test: the shaker. It vibrates the experiment assembly to determine its Eigenfrequencies and to see if the assembly can withstand the launch loads. Peak forces of 20G are reached during the test.
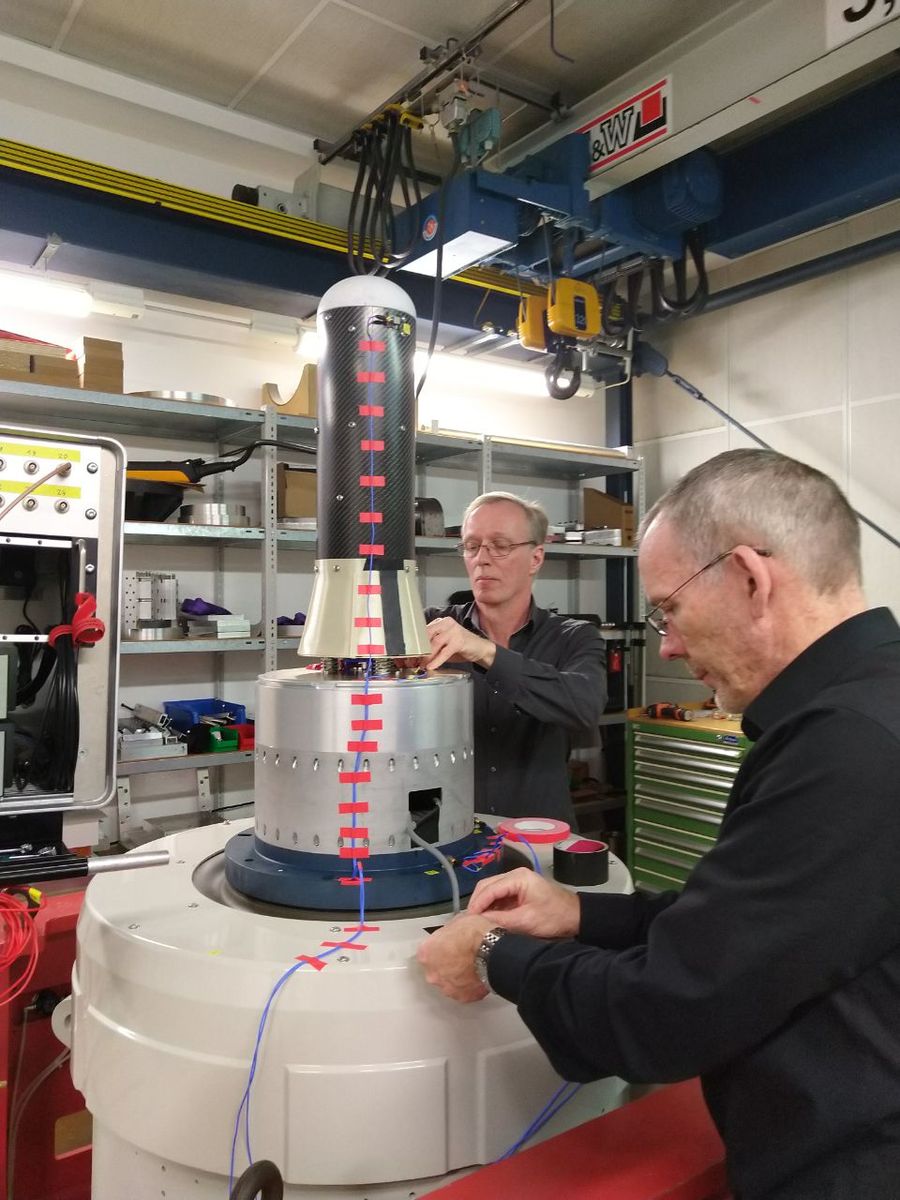
Test engineers of ZARM fix the assembly (including the bulk head) to the shaker and attach accelerometers.
And gladly, we passed the vibration test. Yay!
Last but not least, a fit check has been done with the rocket's nosecone to clearly verify that we actually fit onto the rocket. And surprise, we also passed this test!
Last but not least, a fit check has been done with the rocket's nosecone to clearly verify that we actually fit onto the rocket. And surprise, we also passed this test!
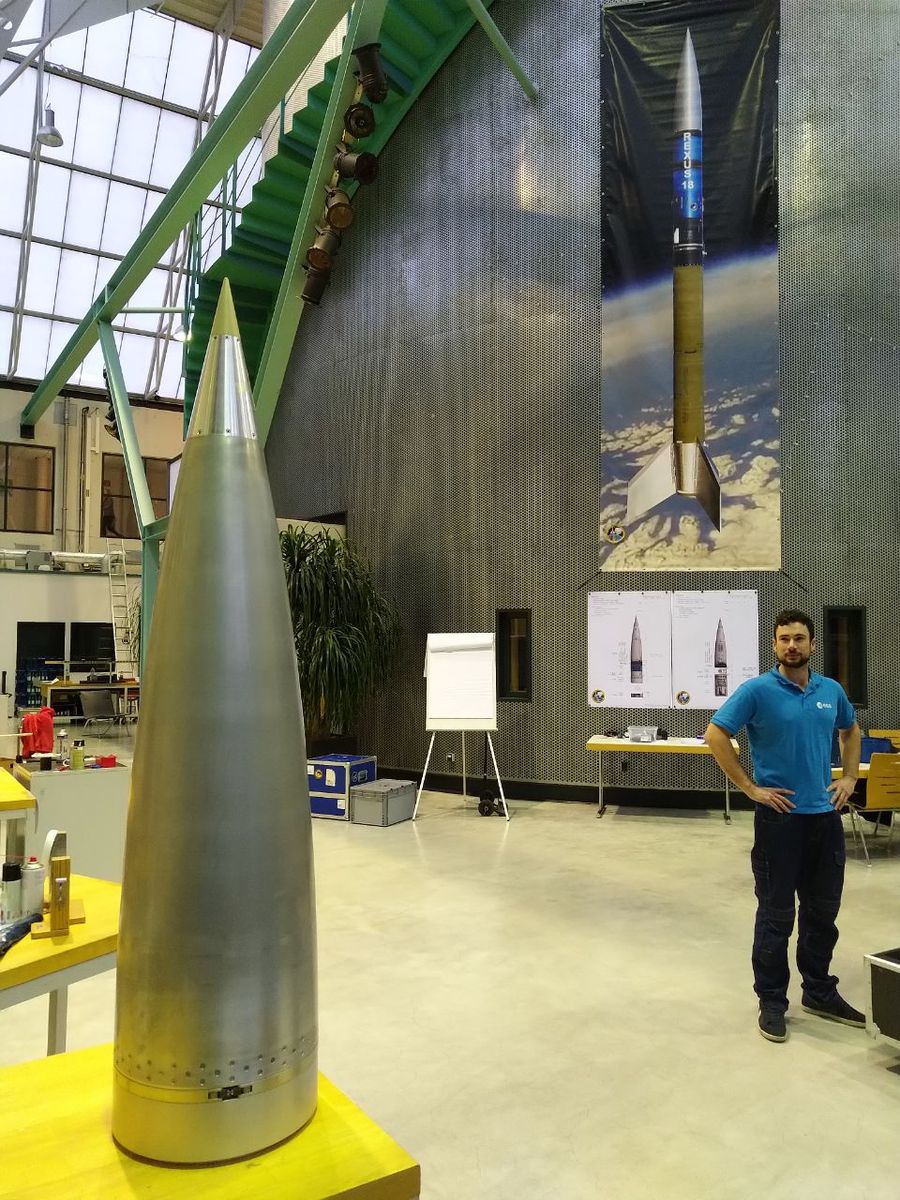
(Have a look at Alex' face. He looks as proud as if he built the experiment by himself! But we have to admit, it looks pretty sexy.)
Now we have to work on our to do list so that we can go to the Bench Test in January fully prepared. Becuase we still didn't really pass the EAR... somewhat we did, but not really. But it will work out, like it always did so far.
Cheers and happy new year,
Cheers and happy new year,
Siiri, Nik, Jaka and Fabian